Double covered yarn has revolutionized the textile industry with its unique construction and versatile applications. This innovative yarn type consists of a core filament wrapped with two layers of fiber, creating a superior textile component that combines strength, elasticity, and aesthetic appeal. The growing demand for double covered yarn across various sectors, from fashion to technical textiles, demonstrates its significant impact on modern fabric production.
Double covered yarn
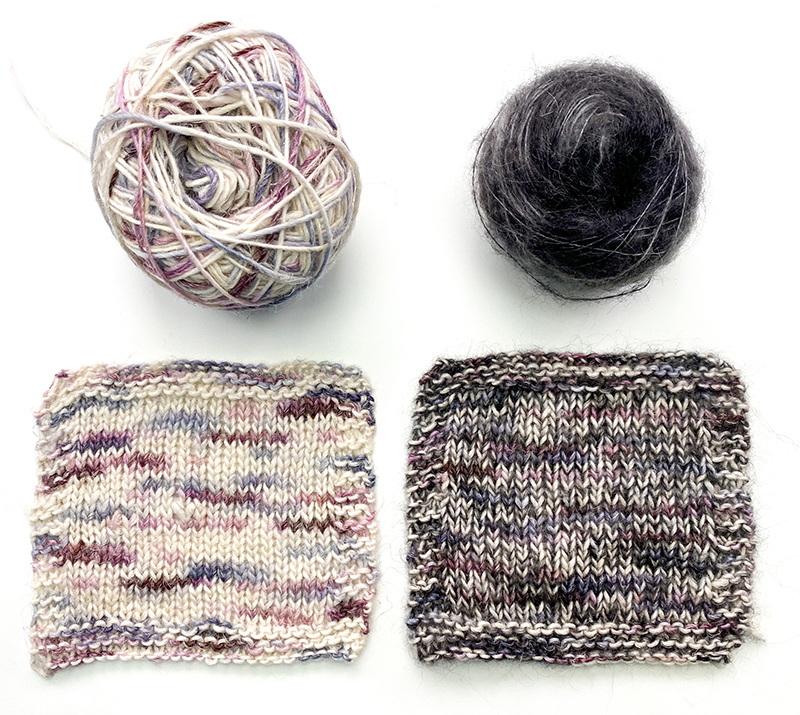
Double covered yarn represents a remarkable achievement in textile engineering, combining multiple fiber layers to create a versatile and robust yarn structure. The manufacturing process involves wrapping a core filament, typically elastane or spandex, with two distinct layers of covering material, resulting in a product that offers superior performance characteristics.
Construction and Manufacturing Process
The production of double covered yarn begins with selecting a high-quality core filament, usually elastane or spandex, which provides the foundation for the yarn’s elasticity. This core is first wrapped with an initial covering layer in one direction, typically using polyester, nylon, or cotton fibers. The second covering layer is then applied in the opposite direction, creating a balanced structure that prevents unwinding and ensures stability.
The precise control of tension during the covering process is crucial for maintaining consistent quality. Advanced machinery equipped with electronic monitoring systems ensures uniform coverage and prevents irregularities that could compromise the yarn’s performance. The speed and tension settings must be carefully calibrated to accommodate different fiber types and achieve the desired characteristics.
Modern manufacturing facilities employ sophisticated quality control measures throughout the production process, including real-time monitoring of yarn parameters and regular testing of physical properties. This attention to detail ensures that each batch of double covered yarn meets stringent quality standards.
Performance Characteristics and Benefits
Double covered yarn exhibits exceptional performance characteristics that set it apart from conventional yarn types. The dual-layer construction provides superior coverage of the elastic core, resulting in enhanced stability and durability. This unique structure prevents the core from breaking through the surface, a common issue with single-covered yarns.
The balanced wrapping of the covering layers contributes to improved dimensional stability and reduced torque in the finished fabric. This characteristic is particularly valuable in producing high-quality stretch fabrics that maintain their shape and recovery properties even after repeated use. The yarn’s structure also enables better moisture management and thermal regulation in the final product.
These performance benefits make double covered yarn ideal for applications requiring both elasticity and durability, such as athletic wear, compression garments, and high-end fashion items. The yarn’s versatility allows designers and manufacturers to create innovative textile products that meet demanding performance requirements.
Applications Across Industries
Double covered yarn finds widespread application across various textile sectors, demonstrating its versatility and adaptability. In the fashion industry, it enables the creation of form-fitting garments that combine comfort with style, particularly in premium denim and activewear. The yarn’s ability to maintain shape and recover from stretching makes it essential for producing high-performance athletic apparel.
The technical textile sector utilizes double covered yarn in medical compression garments, where precise pressure control and durability are crucial. Industrial applications benefit from the yarn’s strength and reliability in products such as automotive upholstery and protective clothing.
The growing demand for sustainable textile solutions has led to innovations in double covered yarn production, including the incorporation of recycled materials and eco-friendly manufacturing processes. This adaptation to market trends ensures the continued relevance of double covered yarn in modern textile manufacturing.
What is double knitting weight yarn
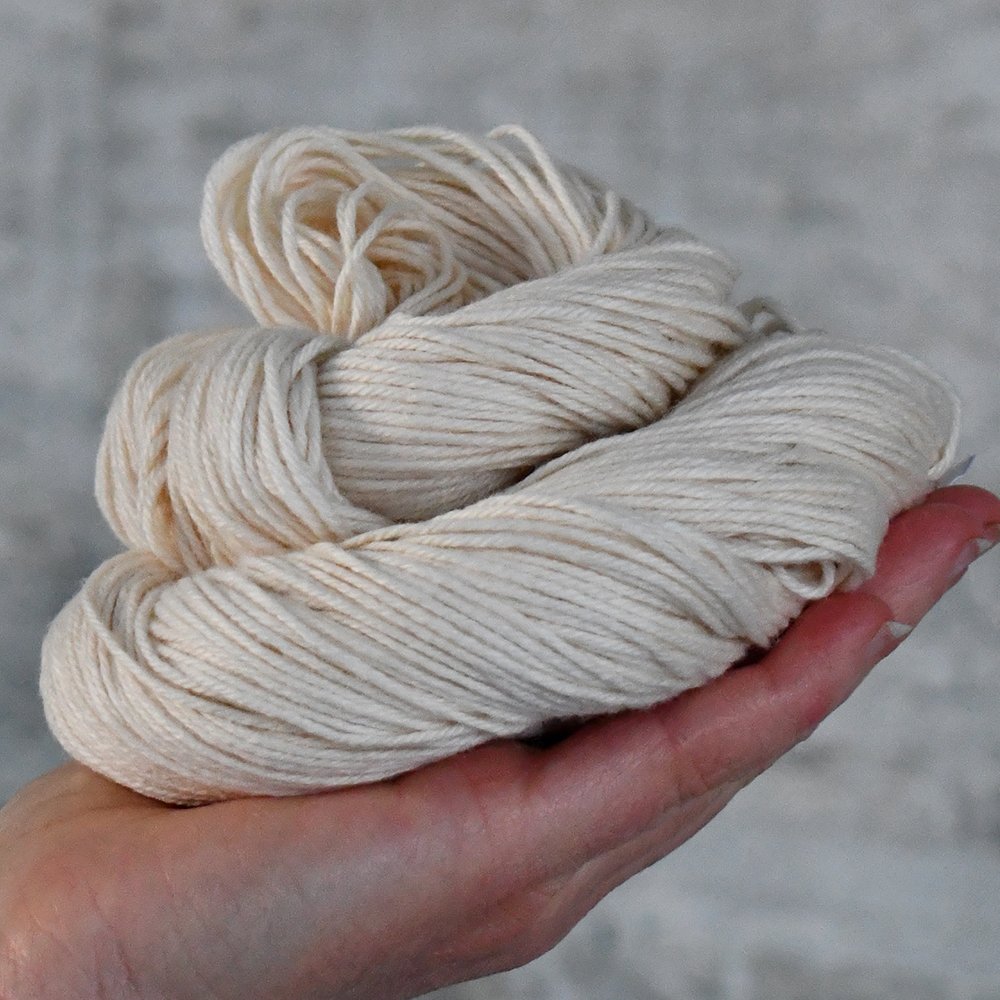
Double knitting weight yarn, often abbreviated as DK, represents a medium-weight yarn category that offers exceptional versatility and handling characteristics. This weight classification has become a standard in the textile industry, particularly in hand knitting and machine knitting applications.
Classification and Standards
Double knitting weight yarn typically falls between sport weight and worsted weight in the standard yarn classification system. The yarn count usually ranges from 11-14 wraps per inch, providing a balanced combination of bulk and manageability that suits a wide range of projects.
Manufacturing standards for double knitting weight yarn ensure consistency across different producers and fiber types. This standardization helps designers and craftspeople achieve predictable results in their projects, whether working with natural fibers, synthetics, or blended yarns.
The classification system takes into account factors such as fiber content, twist level, and finishing processes, all of which contribute to the yarn’s final characteristics and performance in different applications. This comprehensive approach to classification ensures that users can confidently select appropriate yarns for their specific needs.
Properties and Characteristics
Double knitting weight yarn exhibits distinct properties that make it particularly suitable for a wide range of textile applications. The balanced weight and structure provide excellent stitch definition, making it ideal for patterns that feature both textural and color work elements.
The yarn’s medium weight contributes to fabric with optimal drape and body, neither too heavy nor too light for most applications. This versatility allows creators to produce garments suitable for various seasons and climates. The structure of double knitting weight yarn also facilitates even stitch formation, resulting in professional-looking finished products.
These yarns typically offer good wear resistance and durability, maintaining their appearance and performance characteristics through regular use and maintenance. The medium weight classification also provides efficient coverage while remaining economical in terms of material usage.
Applications and Project Suitability
Double knitting weight yarn excels in a broad range of applications, from garments to home accessories. Its versatility makes it particularly suitable for creating sweaters, cardigans, and accessories that require both warmth and drape. The medium weight provides enough substance for structural elements while maintaining flexibility in design implementation.
The yarn performs exceptionally well in projects requiring detailed stitch patterns or colorwork, as its structure allows for clear stitch definition and smooth color transitions. This characteristic makes it popular among designers and crafters who want to showcase intricate pattern work.
For machine knitting applications, double knitting weight yarn offers reliable performance and compatibility with a wide range of machine gauges. This adaptability makes it a preferred choice for both domestic and industrial knitting operations.
Is medium weight yarn double knit
The relationship between medium weight yarn and double knitting is often a source of confusion in the textile industry. While these terms are sometimes used interchangeably, they actually refer to different aspects of yarn classification and construction.
Understanding Weight Classifications
Medium weight yarn encompasses a range of yarn weights that fall between light and heavy categories. This classification system helps standardize yarn selection across different manufacturers and applications. The weight category directly influences the yarn’s behavior in various projects and its suitability for specific techniques.
Weight classifications take into account factors such as fiber density, twist level, and overall yarn diameter. These characteristics collectively determine how the yarn will perform in different applications and what gauge or tension will be appropriate for optimal results.
Modern textile manufacturing has developed precise methods for measuring and categorizing yarn weights, ensuring consistency across different production batches and manufacturers. This standardization benefits both industrial producers and individual crafters by providing reliable guidelines for project planning and execution.
Relationship Between Weight and Construction
Medium weight yarns can be produced using various construction methods, including single ply, multiple ply, and specialty techniques. The construction method significantly influences the yarn’s properties and performance characteristics, independent of its weight classification.
The term “double knit” specifically refers to a knitting technique or fabric structure, rather than the weight or construction of the yarn itself. This distinction is crucial for understanding how different yarns can be used in double knitting projects, regardless of their weight classification.
Understanding these relationships helps makers select appropriate yarns for specific projects, considering both the desired weight and the intended construction technique. This knowledge enables better project planning and more successful outcomes.
Selection Criteria and Considerations
Choosing between different medium weight yarns requires careful consideration of multiple factors, including the intended use, desired fabric characteristics, and specific project requirements. The selection process should account for both the yarn’s weight classification and its construction method.
Project success often depends on matching the yarn’s characteristics with the intended application and technique. Factors such as stitch definition, drape, and wear resistance play crucial roles in determining the most suitable yarn for a particular project.
Professional designers and manufacturers consider additional factors such as cost efficiency, availability, and consistency when selecting yarns for commercial production. These considerations ensure that the chosen materials meet both technical requirements and practical constraints.
Conclusion
Double covered yarn has proven itself as a fundamental component in modern textile manufacturing, offering unique benefits that contribute to high-performance fabrics and innovative textile solutions. The combination of strength, elasticity, and versatility makes it an indispensable material across various applications, from fashion to technical textiles.
The clear distinctions between yarn weights, construction methods, and knitting techniques provide a framework for understanding how different yarn types can be effectively utilized. This knowledge enables better decision-making in both industrial and craft applications, leading to superior finished products that meet specific performance requirements.
As textile technology continues to evolve, the role of double covered yarn remains significant, adapting to new challenges and requirements while maintaining its core advantages. The ongoing development of sustainable production methods and innovative applications ensures its continued relevance in the future of textile manufacturing.
Support by us