Rubber covered yarn is transforming the textile industry, offering enhanced durability, flexibility, and resistance to wear and tear. It has become a preferred choice for various applications, from industrial fabrics to consumer goods. In this article, we will explore the intricacies of rubber covered yarn, its benefits, and its potential to revolutionize materials in various sectors.
Rubber covered yarn
Rubber covered yarn is a specialized type of yarn coated with a layer of rubber, which significantly enhances its physical properties. The process of coating the yarn with rubber provides increased resistance to abrasion, moisture, and chemical exposure compared to traditional fibers. This unique combination allows manufacturers to create products that can withstand demanding environments, making rubber covered yarn a vital component in sectors ranging from automotive to apparel.
The fundamental purpose of rubber covering is to provide a protective layer that extends the life of the yarn while maintaining its inherent elasticity. The resulting product is not only durable but also versatile, allowing it to be woven into various fabrics that can be used for countless applications.
Industries are increasingly recognizing the advantages of rubber covered yarn, leading to a growing demand for this innovative material. As technology advances, manufacturers are able to produce rubber covered yarn that is even more durable and adaptable, responding to the dynamic needs of the market.
The impact of rubber covered yarn on product performance cannot be overstated. When comparing it to standard fibers, rubber covered yarn stands out in terms of durability and longevity, making it ideal for environments where standard materials would fail. Furthermore, the potential for customization in terms of rubber type and coating thickness opens up avenues for specialized applications.
The interplay of elasticity and strength in rubber covered yarn allows textiles to be used in high-stress situations without sacrificing performance. For many industries, this means the difference between a viable product and one that fails prematurely. Consequently, businesses have a compelling reason to invest in rubber covered yarn for their manufacturing processes.
Applications in Various Sectors
Rubber covered yarn is increasingly being employed in a multitude of sectors, each leveraging its unique properties.
The automotive industry, for instance, has adopted rubber covered yarn for seat upholstery, weather seals, and safety belts. The robust nature of this yarn contributes not only to vehicle longevity but also enhances driver and passenger safety. The flexible nature of the rubber-coating allows these components to maintain their shape and integrity over time, regardless of exposure to moisture or temperature fluctuations.
In the realm of sports and outdoor gear, manufacturers are utilizing rubber covered yarn to enhance the durability of products like tents, backpacks, and protective clothing. The ability of rubber to repel water while remaining breathable is crucial in environments where moisture control is essential.
Healthcare textiles also benefit significantly from rubber covered yarn. Medical devices and wearables, such as bandages and support braces, benefit from the material’s anti-bacterial properties and resistance to bodily fluids. These attributes offer not just comfort to the wearer but enhanced hygiene, making them invaluable in a healthcare setting.
Increased Longevity and Versatility
One of the most appealing features of rubber covered yarn is its impressive longevity. By incorporating rubber into the yarn structure, manufacturers extend the life cycle of the textiles produced. A longer life cycle reduces waste and promotes sustainability in production processes, a significant selling point in today’s environmentally conscious market.
The versatility of rubber covered yarn is equally remarkable. It can be used in both high-tech applications and everyday consumer products, broadening its market reach. From heavy-duty industrial applications to comfortable clothing, the adaptability of this material makes it a game-changer in textile manufacturing.
The rubber coating can also be tailored for various functions, allowing manufacturers to create specialized products that meet the specific needs of their customers. This customization potential is particularly appealing in industries requiring bespoke solutions that can withstand unique environmental challenges.
Understanding Manufacturing Techniques
The creation of rubber covered yarn involves intricate manufacturing processes that significantly contribute to the quality and performance of the finished product. The layering techniques used when applying rubber to the yarn can alter the properties of the final product, making it essential for manufacturers to choose the right method based on their end use.
Different coating techniques, such as dip coating, extrusion, and spray coating, each have their advantages. Dip coating offers thorough coverage, while extrusion allows for a more uniform layer of material. The choice of rubber also plays a critical role in determining the properties of the rubber covered yarn, including elasticity and resistance to various elements.
Quality control during the manufacturing process is paramount. Each stage— from yarn production to rubber coating—requires meticulous oversight to ensure that the final product meets the high standards expected in industries where performance is critical. This level of diligence helps build trust with manufacturers and consumers alike, who rely on the durability and reliability of rubber covered yarn.
Rubber coated yarn
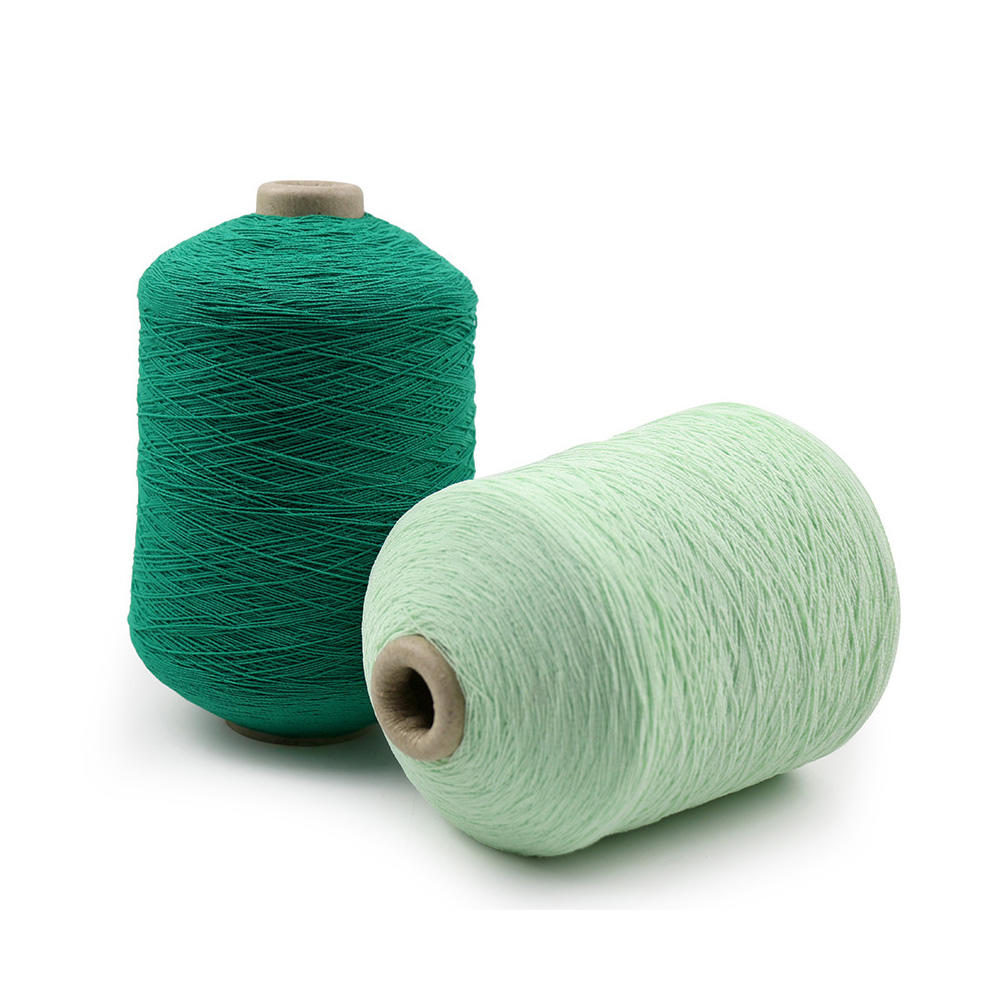
Rubber coated yarn is a versatile material, often confused with rubber covered yarn but possessing notable differences that can impact their functionalities. Understanding these distinctions is imperative for industries considering the use of either material in their products.
Rubber coated yarn essentially refers to the process where a layer of rubber is applied to traditional yarn, creating a composite material that benefits from the unique properties of both fibers and rubber. This method enhances not only durability but can also improve other characteristics like water resistance, flexibility, and overall resilience.
This material is widely used in the production of textiles that demand resistance to elongation and strain. Industries that require durable and flexible products often turn to rubber coated yarn to ensure that their materials can withstand the rigors of their applications.
Crafting a Durable Composite
The composition of rubber coated yarn plays a pivotal role in its overall performance. The method chosen for applying the rubber coating can significantly influence how the yarn behaves under stress or environmental challenges.
For example, when using a thicker rubber layer, the resulting product may excel in abrasion resistance but may sacrifice flexibility. Conversely, a thinner layer might allow for more stretch but might not provide the same level of protection.
Manufacturers must strike a careful balance between durability and usability, which is where understanding the end application becomes vital. The specific requirements of each industry dictate the appropriate thickness and type of rubber used, ensuring that the resulting yarn meets performance expectations.
Industry-Specific Use Cases
Various industries have adopted rubber coated yarn to enhance their product offerings, with each sector integrating the material in ways tailored to their unique needs. For instance, in the marine industry, rubber coated yarn is popular due to its resistance to saltwater and UV damage, making it ideal for outdoor applications.
In the field of personal protective equipment, such as gloves and harnesses, the elasticity provided by rubber coated yarn is invaluable. It allows for a snug fit without sacrificing movement, providing safety while maintaining comfort.
The textile fashion industry has also begun to explore the potential of rubber coated yarn, incorporating the material into garments that require a mix of style and performance. This trend has led to innovative designs that leverage the aesthetic qualities of textiles while ensuring durability in everyday wear.
Performance Benefits
The performance benefits of rubber coated yarn are significant, particularly in demanding conditions. The moisture resistance offered by rubber allows it to function well in environments exposed to water and humidity. This is particularly relevant in industries like agriculture and sports, where equipment is regularly subjected to harsh weather.
Additionally, the chemical resistance of rubber coated yarn broadens its applicability, making it suitable for environments where exposure to oils, greases, and other chemicals is possible. These features make it an ideal candidate for products used in hazardous conditions, elevating the safety and longevity of necessary equipment.
The use of rubber coated yarn also contributes to the overall performance of composite materials when combined with traditional textiles. This creates new opportunities for hybrid products that leverage the strengths of both fiber types, paving the way for innovations that alter how textiles are manufactured and used.
Rubber yarn covering machine manufacturer
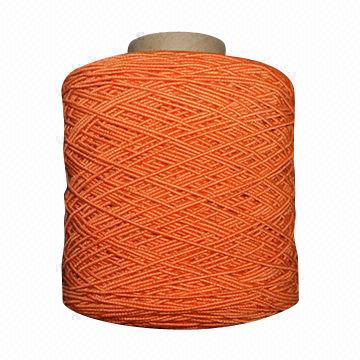
The production of rubber covered and rubber coated yarn requires specialized machinery capable of applying the rubber layer uniformly and effectively. This aspect of manufacturing is critical, as the quality of the equipment directly influences the performance characteristics of the finished product.
Rubber yarn covering machine manufacturers play a vital role in this segment of the textile industry. With advancements in technology, the machines they design must not only be efficient but also adaptable to different types of yarn and rubber materials. This adaptability ensures that manufacturers can respond to market demands for varied applications seamlessly.
The Engineering Behind Yarn Covering Machines
The design and engineering of rubber yarn covering machines involve an intricate understanding of both material science and mechanical processes. The machines must deliver precise amounts of rubber on the yarn while maintaining consistent tension to avoid weakening the fiber.
Different types of machines are available, each suited for specific production needs. Some machines excel in high-speed applications, delivering large volumes of coated yarn efficiently, while others prioritize versatility, allowing for diverse coating types and thicknesses.
Investing in high-quality machinery is crucial for manufacturers aiming to produce distinct rubber covered yarn products. Choosing the right machine can lead to enhanced production rates and improved quality control, ultimately resulting in a superior final product.
Trends in Machinery Technology
The technological landscape surrounding the manufacturing of rubber covered yarn is evolving rapidly. Automation and digitization are becoming commonplace in production processes, enabling manufacturers to enhance efficiency and reduce human error.
Many machines now incorporate smart technology that allows for real-time monitoring and adjustments during production. This capability ensures higher consistency across batches and reduces the potential for defects, ultimately translating into reduced costs and higher customer satisfaction.
The trend toward sustainability in manufacturing is also influencing machine design. Modern machines are being developed with energy efficiency in mind, allowing manufacturers to reduce emissions and operational costs. Combining these advancements with the growing use of eco-friendly materials in yarn production represents a significant step toward a more sustainable future.
Supplier-Client Relationships
Building strong relationships between rubber yarn covering machine manufacturers and their clients is fundamental to achieving mutual success. Manufacturers must understand their clients’ goals and production challenges to provide tailored solutions that meet specific needs.
Furthermore, ongoing support and maintenance of machinery are crucial to keeping the production lines running smoothly. Manufacturers that prioritize customer service, offering training and technical support, are often regarded as leaders in the industry.
These relationships not only facilitate immediate business dealings but also create pathways for innovation and collaboration. When manufacturers and clients work hand in hand, they open doors to new techniques and materials that can push the boundaries of what rubber covered yarn can achieve.
Is rubber breathable
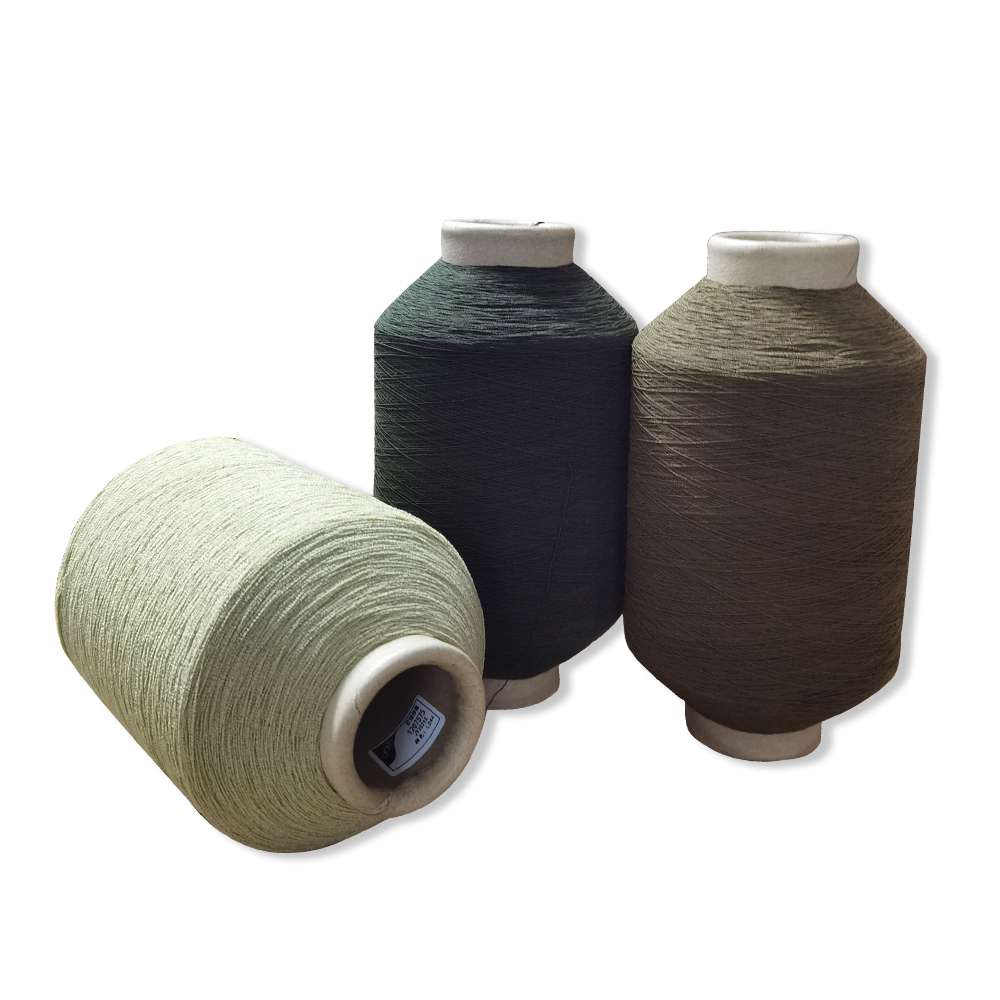
One common question that arises in discussions about rubber materials is whether rubber is breathable. The answer varies depending on the type and formulation of rubber used, making it a nuanced topic worthy of exploration.
In general, traditional rubber is considered non-breathable due to its dense molecular structure, which creates a barrier against air and moisture. This characteristic can be beneficial in applications where water resistance is required, such as in protective clothing and bedding.
However, advancements in technology have led to the development of breathable rubber formulations. These types of rubber incorporate specialized designs to allow for air permeability without sacrificing water resistance. Breathable rubber is a game changer for various applications, including sportswear and footwear, as it helps regulate temperature and moisture, ultimately improving comfort for the wearer.
Applications of Breathable Rubber
Breathable rubber finds significant use in products where comfort is paramount. In outdoor apparel, for instance, brands are increasingly integrating breathable rubber into their waterproof jackets and trousers, ensuring that wearers remain dry while also allowing perspiration to escape.
In the footwear sector, breathable rubber is making waves by improving comfort for athletes and everyday consumers. Shoes equipped with breathable rubber soles allow for ventilation, reducing moisture buildup and helping to prevent bacterial growth and unpleasant odors.
Medical applications also benefit from breathable rubber materials, particularly in garments worn for extended periods. This includes compression suits and supports, which need to allow air flow to maintain comfort while providing effective support.
Challenges and Solutions
While the concept of breathable rubber may seem advantageous, there are challenges associated with its use. Achieving the ideal balance between breathability, durability, and water resistance can be a complex task, often requiring rigorous testing and innovation in material formulations.
Manufacturers constantly experiment with blends of rubber materials and the incorporation of microporous structures to achieve the desired balance of properties. Continuous research is aimed at overcoming these challenges, opening new possibilities for both performance and comfort in textiles.
The future of breathable rubber is promising, with ongoing advancements leading to new applications and increased consumer demand. As manufacturers continue to innovate, we can expect to see even more products that harness the benefits of breathable rubber.
Conclusion
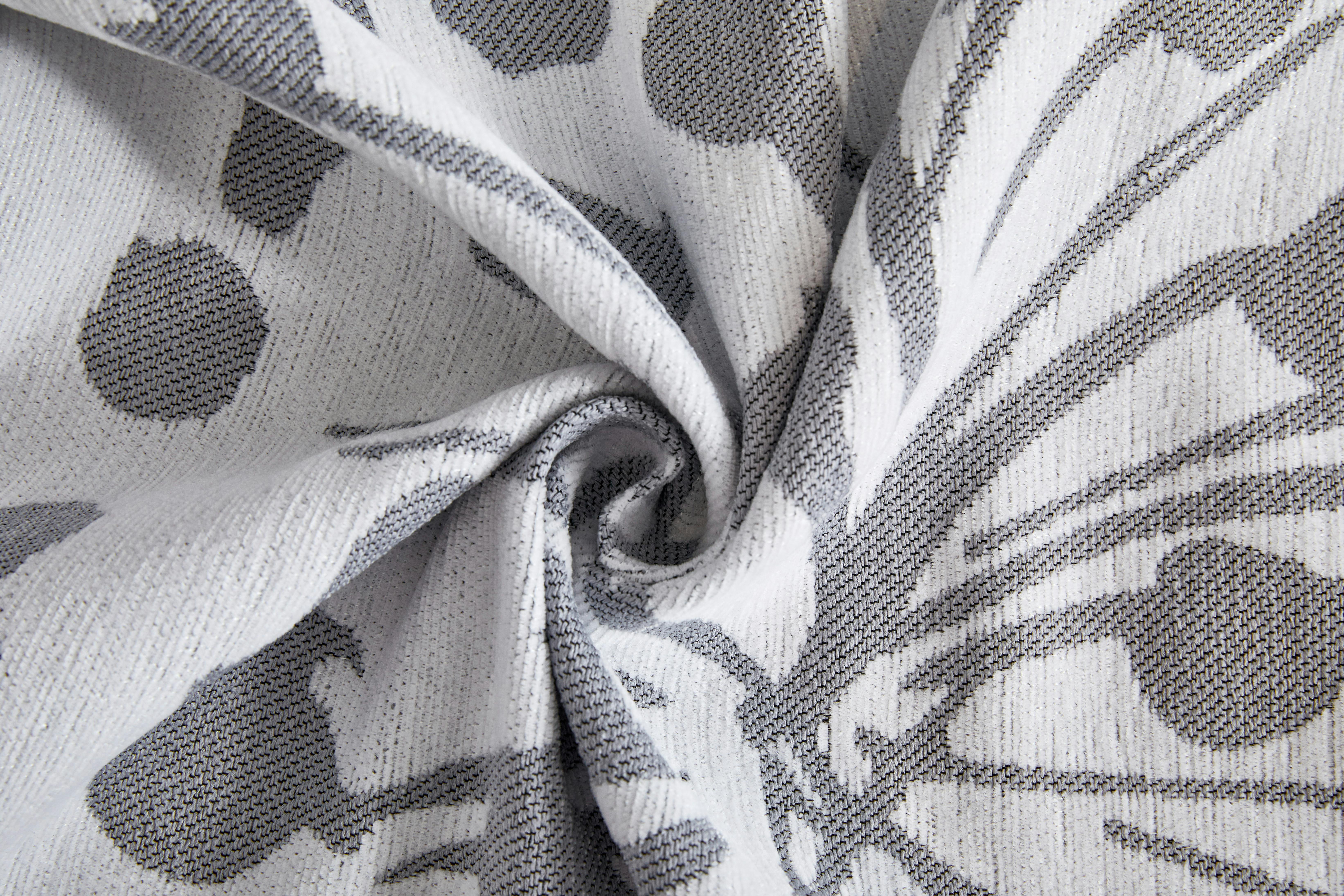
In summary, rubber covered yarn and its related offerings, such as rubber coated yarn, represent a significant advancement in textile innovation. Their remarkable properties of durability, flexibility, and adaptability have led to their adoption across various industries, enhancing product performance in countless applications.
The technology behind rubber yarn covering machines continues to evolve, ensuring manufacturers can meet the growing demands for high-quality, specialized yarns. With the ongoing exploration of breathable rubber and its potential applications, it is clear that the future of rubber in textiles is bright.
As industries continue to prioritize longevity, performance, and sustainability, rubber covered yarn stands at the forefront, poised to shape the future of textiles. Embracing these innovations will undoubtedly lead to improved products and experiences for consumers and manufacturers alike.
sourcing by us