Rubber covered yarn represents a revolutionary advancement in textile manufacturing, combining the elasticity of rubber with the strength and versatility of traditional yarn materials. This innovative composite material has transformed various industries, from clothing to industrial applications, by offering unique properties that enhance product performance and durability.
Keywords: rubber covered yarn, what is rubber fabric, what is rubber material, is rubber a textile material, why is rubber a good material
Rubber Covered Yarn
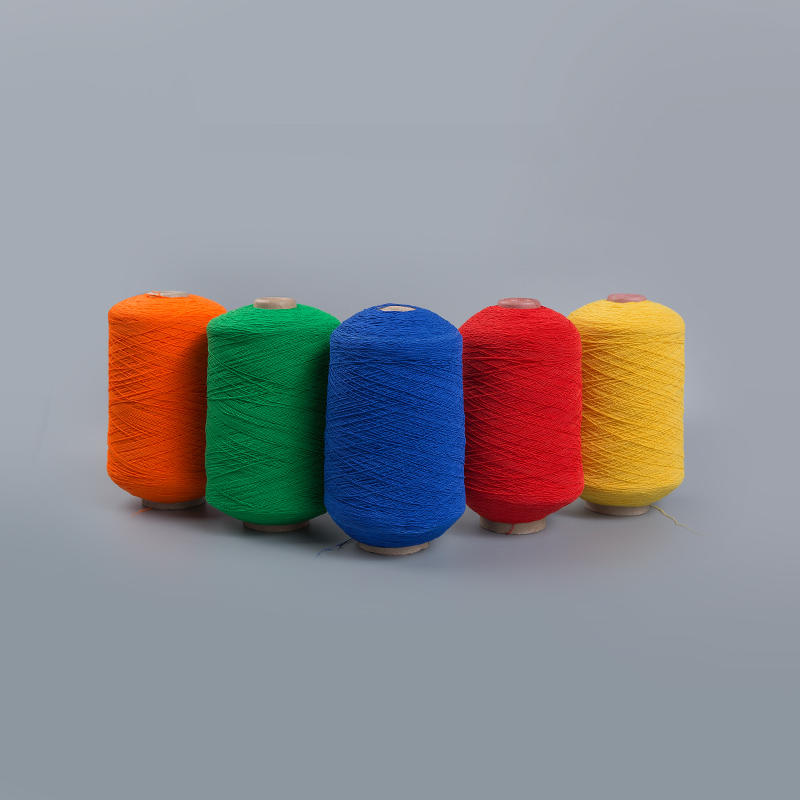
The evolution of rubber covered yarn technology has revolutionized the textile industry, offering unprecedented flexibility and durability in manufacturing processes. This innovative material combines traditional yarn cores with rubber coating techniques to create a versatile product that serves multiple industrial and consumer applications.
Manufacturing Process and Technology
The production of rubber covered yarn involves a sophisticated process where base yarns, typically polyester or nylon, undergo specialized rubber coating procedures. This process begins with carefully selecting core materials based on intended applications and desired characteristics.
The coating process utilizes advanced machinery that precisely controls rubber application thickness and consistency. Modern manufacturing facilities employ temperature-controlled environments and specialized equipment to ensure optimal adhesion between the rubber coating and core yarn structure.
Quality control measures throughout the manufacturing process include continuous monitoring of coating thickness, elasticity testing, and durability assessments to maintain consistent product specifications.
Applications and Industry Usage
Rubber covered yarn finds extensive applications across diverse industries, particularly in technical textiles and specialized garment manufacturing. The automotive sector utilizes this material in seat belts and airbag components, where consistent performance under stress is crucial.
In the medical industry, these yarns contribute to the production of compression garments and therapeutic wear. Their ability to maintain elastic properties while providing comfort makes them ideal for these applications.
The sporting goods industry has embraced rubber covered yarn for producing high-performance athletic wear, where moisture management and flexibility are essential requirements.
Performance Characteristics
The unique combination of rubber and yarn creates exceptional performance characteristics that distinguish this material from conventional textile products. These yarns exhibit superior elastic recovery, maintaining their shape and functionality even after repeated stretching.
Moisture resistance and environmental durability are key advantages, as the rubber coating provides protection against various environmental factors while maintaining the base yarn’s integrity. The material also demonstrates excellent resistance to abrasion and wear, contributing to extended product lifespans.
Temperature stability and chemical resistance further enhance the material’s versatility, making it suitable for applications in challenging environments.
What Is Rubber Fabric
,aspect=fit)
Rubber fabric represents a significant innovation in textile engineering, combining the properties of traditional fabrics with the unique characteristics of rubber materials. This hybrid material has transformed how we approach technical textile applications and performance wear.
Composition and Structure
The fundamental structure of rubber fabric involves a complex integration of rubber compounds with textile substrates. Manufacturers utilize various techniques to bond rubber elements with fabric bases, creating materials with specific performance characteristics.
The selection of base fabrics and rubber compounds significantly influences the final product’s properties. Different rubber formulations can be employed to achieve specific characteristics such as flexibility, durability, or weather resistance.
Advanced manufacturing processes ensure uniform distribution of rubber components throughout the fabric structure, maintaining consistent performance across the material.
Properties and Characteristics
Rubber fabric exhibits distinct properties that set it apart from conventional textiles. The material demonstrates exceptional elasticity while maintaining dimensional stability, making it ideal for applications requiring both flexibility and form retention.
Weather resistance and waterproofing capabilities are enhanced by the rubber component, while the fabric base maintains breathability where required. This balance of properties makes rubber fabric particularly valuable in outdoor and technical applications.
The material’s ability to resist wear and tear while maintaining its protective properties contributes to its popularity in demanding applications.
Manufacturing Techniques
Modern rubber fabric production employs sophisticated manufacturing methods that ensure precise control over material properties. Various coating and lamination techniques are utilized to achieve specific performance characteristics.
Quality control processes throughout manufacturing ensure consistency in rubber distribution and adhesion. Advanced testing methods verify the material’s performance under various conditions, ensuring it meets intended specifications.
The manufacturing process incorporates environmental considerations and sustainability practices, reflecting growing industry awareness of ecological responsibilities.
What Is Rubber Material
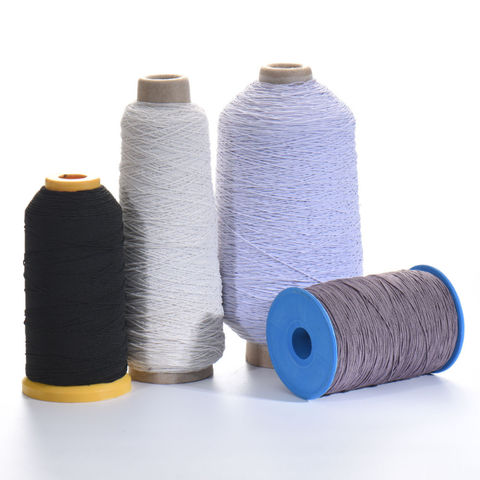
Rubber material encompasses a diverse family of elastomeric compounds that have transformed various industries through their unique properties and versatile applications. Understanding the fundamental nature of rubber materials is crucial for their effective utilization in manufacturing processes.
Chemical Composition and Types
Natural rubber, derived from Hevea brasiliensis trees, consists primarily of polyisoprene chains that provide its characteristic elasticity. This organic compound undergoes various treatment processes to enhance its properties.
Synthetic rubbers, developed to meet specific industrial requirements, offer customizable properties through careful molecular design. Different types include styrene-butadiene rubber (SBR), nitrile rubber (NBR), and ethylene propylene rubber (EPDM).
Modern rubber compounds often incorporate various additives and reinforcing agents to enhance specific properties such as strength, durability, or heat resistance.
Physical Properties and Behavior
The unique molecular structure of rubber materials enables their distinctive elastic behavior and recovery properties. Understanding these characteristics is essential for appropriate material selection in various applications.
Temperature response and aging characteristics significantly influence rubber material performance over time. Manufacturers must consider these factors when designing products for specific environmental conditions.
The material’s response to stress, strain, and environmental factors determines its suitability for different applications and influences product design decisions.
Processing Methods
Rubber processing involves various techniques that transform raw materials into usable products. These methods include mixing, molding, extrusion, and vulcanization processes.
Advanced processing technologies enable precise control over material properties and performance characteristics. Quality control measures throughout processing ensure consistent product quality and reliability.
Continuous innovation in processing methods has led to improved efficiency and enhanced material properties, expanding the potential applications for rubber materials.
{
Applications Across Industries
The rubber material family is utilized across various sectors, including automotive, aerospace, medical, and consumer goods. Its unique properties make it suitable for components requiring flexibility combined with durability.
In the automotive sector, rubber materials are integral to tire manufacturing, seals, and gaskets, where their tensile strength and resilience are critical for functionality. In the aerospace industry, rubber compounds are employed in sealing systems and vibration dampers, underscoring their contribution to safety and performance under rigorous conditions.
Moreover, in healthcare, rubber materials are essential in creating products such as gloves and medical tubing, where hygiene and flexibility are paramount. The adaptability of rubber makes it indispensable in countless applications.
Is Rubber a Textile Material
The classification of rubber as a textile material is nuanced and subject to interpretation within the fabric and material science realms. Although traditionally not regarded as a textile, the integration of rubber with fibers has led to its recognition in certain applications.
Defining Textiles
Textiles are generally defined as flexible materials consisting of interlaced fibers, used to create fabrics that serve a multitude of functions. These functions range from aesthetics to utility in clothing, home wares, and industrial uses.
While rubber does not fall under the traditional definition of textile due to its inherent solid state, its amalgamation with fibers can produce hybrid materials like rubber-covered yarn that extend the scope of textiles into new territories of application and design.
Hybrid Materials
Rubber’s combination with fibers calls for reevaluation of material classifications. Hybrid textiles bring together the durability and elasticity of rubber with the aesthetic and functional properties of traditional fabrics, broadening the horizons of what constitutes a textile.
Fashion designers have embraced this evolution, designing collections featuring rubber-infused garments that prioritize both style and performance. This collaboration fosters innovation in materials science and fashion, where the boundaries of utility and creativity continuously shift.
Acceptance in Fashion and Industry
There is an increasing acceptance of rubber and its blends as valid contributors to the textile community, particularly in technical and performance wear sectors. Research and development efforts focus on enhancing the synergy between rubber and various fiber types, yielding a new generation of materials tailored for specific functions.
This transition reflects the evolving attitudes toward sustainability, wearability, and functionality in fabric development, where the incorporation of rubber allows for eco-friendlier products built to last.
Why Is Rubber a Good Material
The merit of rubber as a material lies in its fundamental properties, showcasing versatility, durability, and performance enhancements across various applications. Understanding these qualities reveals why rubber remains a top choice for numerous industries.
Elasticity and Resilience
One of the hallmark traits of rubber is its exceptional elasticity, allowing it to stretch significantly without permanent deformation. This property makes rubber ideal for applications requiring significant movement and flexibility while returning to its original shape after the load is lifted.
In practice, this quality translates well in products such as elastic bands, seals, and gaskets. The ability to withstand repetitive stress while retaining structural integrity contributes to increased product longevity and reliability, further cementing rubber’s status as a vital material across industries.
Environmental Resistance
Rubber also offers remarkable resistance to environmental factors including temperature fluctuations, moisture, chemicals, and UV radiation. This resistance not only enhances the usability of products but also ensures that they remain functional and aesthetically pleasing over time.
For instance, in outdoor applications, rubber’s weather resistance prevents degradation caused by sunlight and rain, making it perfect for everything from tires to outdoor gear. This durability means fewer replacements, resulting in increased sustainability within various product cycles.
Performance Capabilities
The unique molecular structure enables rubber to exhibit varied performance capabilities based on required specifications. Whether it’s being molded into intricate designs or formulated to meet precise industrial requirements, rubber’s adaptability enhances its appeal.
Furthermore, advancements in rubber technology constantly evolve its properties, enabling manufacturers to tailor materials to meet the stringent demands of modern consumers. The exploration of new formulations continues to push the envelope of what rubber can achieve, ensuring its relevance in future innovations.
Conclusion
In conclusion, the exploration of rubber covered yarn, rubber fabric, rubber material, its classification within textiles, and the underlying benefits demonstrate the multifaceted nature of rubber as an integral component of the modern fabric landscape. As industries continue to innovate and adapt, rubber will undoubtedly maintain its pivotal role in developing new products that balance practicality with creative expression. Embracing rubber’s unique properties opens up exciting possibilities for both manufacturers and consumers alike, driving sustainable practices through multifunctional design.
The fusion of rubber with traditional textiles illustrates a transformative era in material science, expanding our perceptions of what textiles can be in the context of fashion, functionality, and sustainability. Ultimately, rubber stands poised to lead breakthroughs in technical textiles, shaping the future of fabric and product design. Through continuous research and innovation, the potential applications for rubber materials will undoubtedly proliferate, revealing untapped realms of efficiency and performance that can benefit society holistically.
Support by us