Understanding Different Types of Covered Elastic Yarn
Covered elastic yarn represents a revolutionary advancement in textile manufacturing, combining elasticity with durability through specialized covering processes. These innovative yarns consist of an elastic core, typically made from materials like spandex or rubber, wrapped with non-elastic fibers such as polyester, nylon, or cotton. The resulting composite yarn delivers both stretch and recovery properties while maintaining the aesthetic and tactile qualities desired in modern textiles.
The Fundamental Structure and Manufacturing Process

The creation of covered elastic yarn involves a sophisticated process that combines engineering precision with material science. This intricate manufacturing technique ensures the production of yarns that meet specific performance requirements across various applications.
Core Material Selection
The foundation of covered elastic yarn begins with selecting the appropriate core material. Spandex, known commercially as Lycra or elastane, dominates the market due to its superior elastic recovery and durability. These core materials undergo rigorous testing to ensure they meet strict elongation and recovery standards.
Modern manufacturers have developed specialized formulations of spandex specifically designed for covered yarn applications. The molecular structure of these materials is engineered to maintain stability during the covering process while providing optimal stretch characteristics in the final product.
The selection process also considers factors like denier weight, breaking strength, and heat resistance, as these properties significantly influence the yarn’s final performance characteristics.
Single Covering Technology
Single covering represents the most basic form of elastic yarn covering technology. This process involves wrapping a single layer of covering fiber around the elastic core in a spiral pattern. The technique requires precise tension control to achieve uniform coverage without compromising the core’s elastic properties.
Modern single covering machines utilize advanced electronic monitoring systems to maintain consistent wrapping tension and speed. This technological advancement has significantly improved the quality and consistency of single-covered elastic yarns compared to older mechanical systems.
The relationship between covering speed and tension must be carefully balanced to prevent core exposure or excessive binding, both of which can compromise the yarn’s performance.
Double Covering Mechanisms
Double covering technology elevates the protection and stability of elastic yarns through a two-stage covering process. This sophisticated approach involves applying two layers of covering material in opposite directions, creating a more stable and uniform product.
The first covering layer establishes the basic protection and structure, while the second layer enhances durability and provides additional control over the elastic properties. This dual-layer system significantly improves the yarn’s resistance to unraveling and provides better shape retention in finished products.
Modern double covering machines incorporate computerized control systems that allow for precise adjustment of both covering layers independently, enabling manufacturers to create yarns with highly specific characteristics.
Performance Characteristics and Quality Parameters
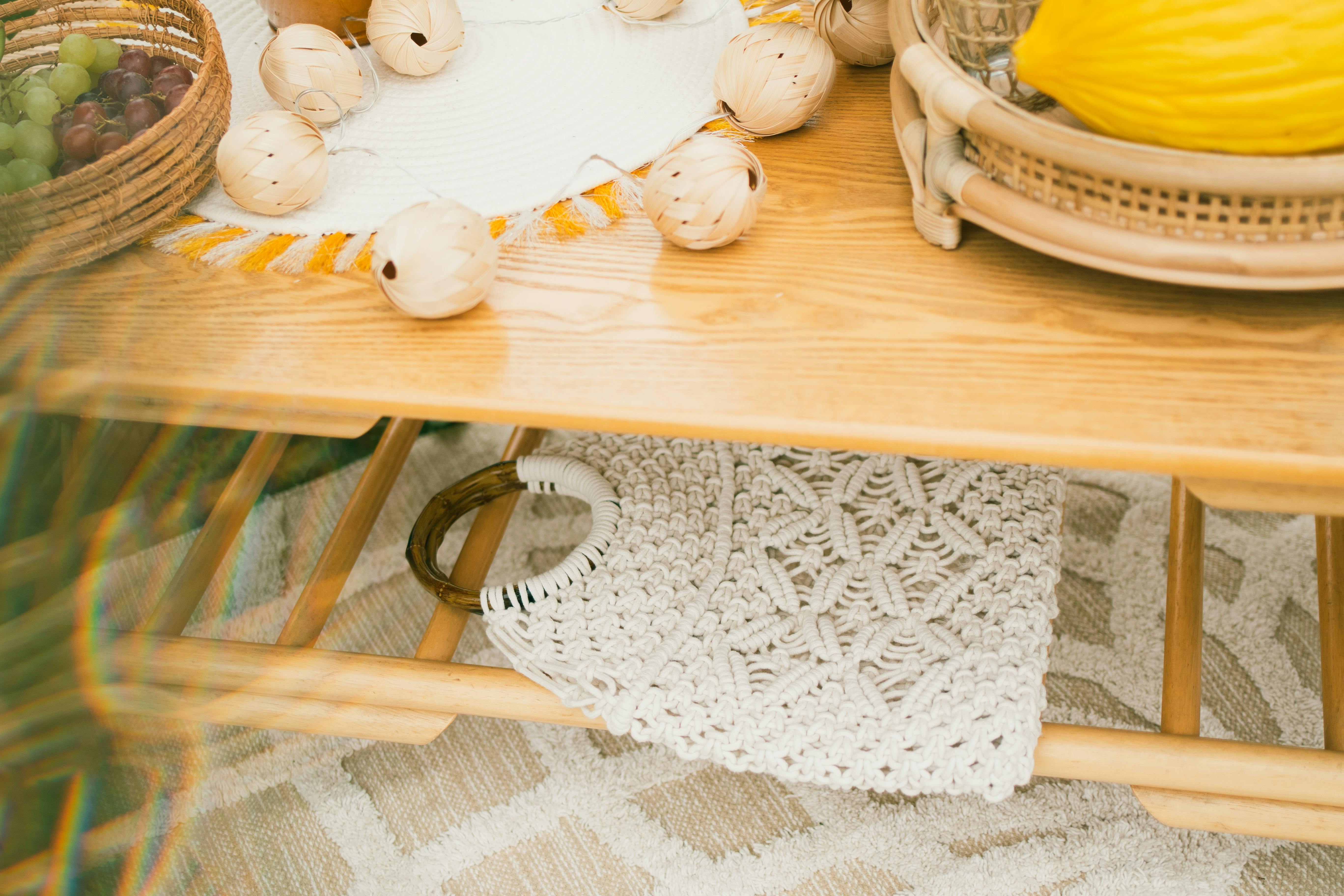
Understanding the performance metrics and quality standards of them is crucial for both manufacturers and end-users. These parameters determine the yarn’s suitability for specific applications and its long-term durability.
Stretch and Recovery Properties
The primary value proposition of covered elastic yarn lies in its ability to stretch and return to its original length. This property is quantified through standardized testing procedures that measure both immediate and long-term recovery characteristics.
High-quality covered elastic yarns typically demonstrate recovery rates above 90% after repeated stretching cycles. This performance metric is particularly crucial in applications like sportswear and compression garments, where consistent pressure application is essential.
Manufacturers continuously work to improve these properties through innovations in both core materials and covering techniques, leading to yarns with increasingly sophisticated performance profiles.
Durability and Wear Resistance
The longevity of covered elastic yarn depends heavily on its resistance to various forms of degradation. This includes resistance to abrasion, chemical exposure, and environmental factors such as UV radiation and temperature fluctuations.
Modern covering techniques have significantly improved the protective qualities of the outer layers, leading to enhanced durability. Special finishing treatments can be applied to further improve resistance to specific environmental challenges.
The interface between the core and covering materials plays a crucial role in determining the yarn’s overall durability, with advanced bonding techniques helping to prevent separation and maintain structural integrity.
Color Fastness and Aesthetic Properties
The ability to maintain visual appeal while delivering functional benefits makes covered elastic yarn particularly valuable in fashion applications. Advanced dyeing techniques ensure color consistency and fastness throughout the product’s lifecycle.
Manufacturers have developed specialized dye formulations that maintain their vibrancy even under repeated stretching. This innovation has expanded the design possibilities for elastic textiles while maintaining performance characteristics.
The covering process must be carefully controlled to ensure uniform dye uptake and consistent appearance, particularly in applications where the yarn will be visible in the final product.
Applications and Market Trends
The versatility of covered elastic yarn has led to its adoption across numerous industries, with new applications continuing to emerge as technology advances. Understanding these trends helps drive innovation in yarn development and manufacturing processes.
Fashion and Apparel Integration
The fashion industry has embraced this yarn as a key component in creating comfortable, form-fitting garments. Modern clothing designs increasingly incorporate these yarns to provide both functionality and style.
Designers are exploring new ways to utilize the unique properties of covered elastic yarns, creating innovative fabric structures that combine comfort with fashion-forward aesthetics. This has led to the development of specialized yarns with varying stretch characteristics and surface textures.
The growing demand for sustainable fashion has also influenced the development of eco-friendly covering materials and manufacturing processes, responding to consumer preferences for environmentally responsible products.
Technical Textile Applications
Technical textiles represent a rapidly growing market for covered elastic yarn, with applications ranging from medical compression garments to aerospace materials. These specialized applications often require highly specific performance characteristics.
Medical textiles, in particular, have benefited from advances in yarn technology, enabling the creation of more effective compression garments and supportive materials. The precise control over pressure application has improved patient outcomes in various therapeutic applications.
Research continues into new technical applications, with developments in smart textiles and responsive materials driving innovation in covered elastic yarn manufacturing.
Athletic and Performance Wear Development
The sports and athletic wear industry has driven significant innovation in covered elastic yarn technology. The demand for high-performance garments that provide both support and freedom of movement has led to the development of increasingly sophisticated yarn variants.
Modern athletic wear incorporates covered elastic yarns with enhanced moisture management capabilities and improved thermal regulation properties. These advances have enabled the creation of garments that actively contribute to athletic performance.
Manufacturers continue to push the boundaries of what’s possible with covered elastic yarn, developing new variants that offer improved comfort and performance characteristics for specific sporting applications.
Conclusion
The evolution of covered elastic yarn technology continues to drive innovation in textile manufacturing, with new applications and improvements emerging regularly. The combination of technical sophistication, performance capabilities, and versatility ensures its position as a crucial component in modern textile production. As manufacturing processes become more advanced and new covering materials are developed, the potential applications for these specialized yarns will continue to expand, promising exciting developments in both technical and fashion applications.
Support by us