The world of textiles is a tapestry woven with countless threads, each with its unique story and purpose. Among these threads, double covered yarn stands out as a testament to human ingenuity and the pursuit of refined textures and enhanced performance in fabrics. This article delves deep into the fascinating world of double covered yarn, exploring its intricate manufacturing process, revealing its unique qualities, and showcasing its diverse applications.
The Anatomy of Double Covered Yarn manufacture: Understanding its Construction
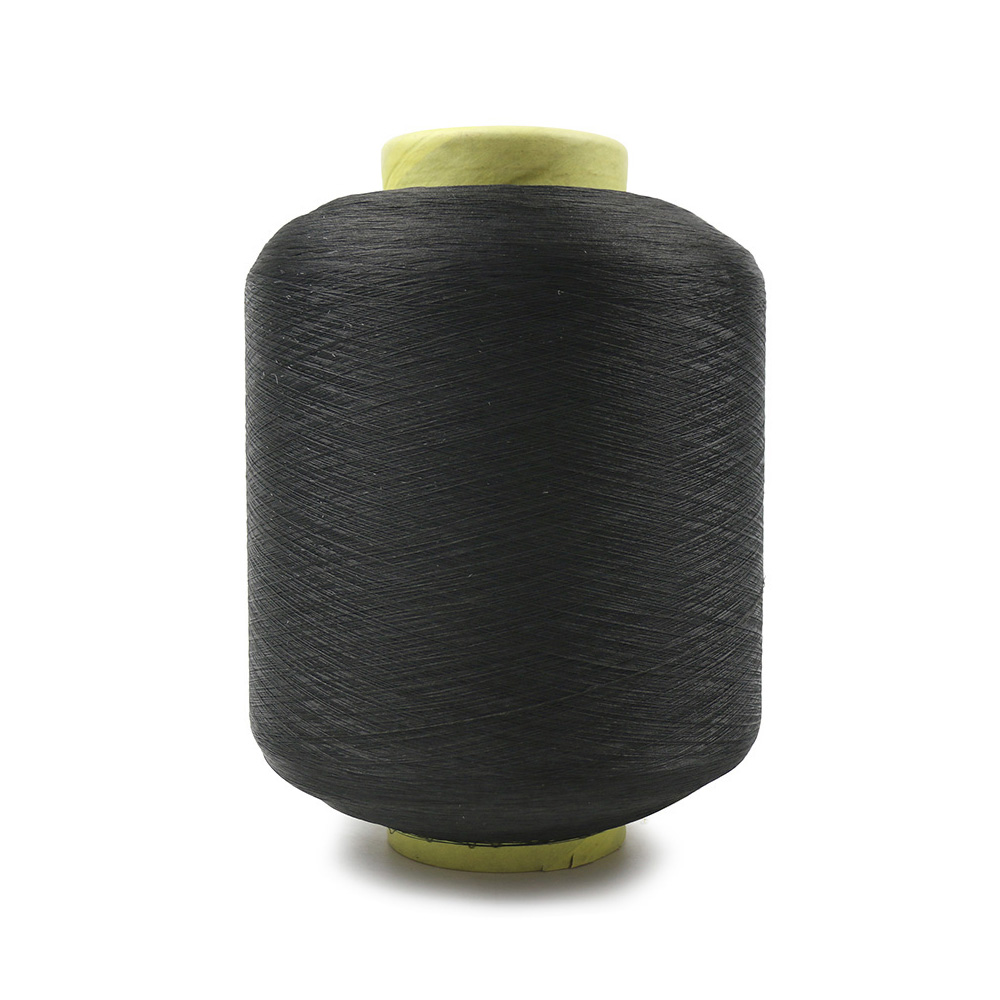
At the heart of double covered yarn lies a core, which is typically a spun yarn made from various fibers. This core yarn is then meticulously wrapped with two layers of covering yarns, creating a robust and versatile material.
The Role of the Core Yarn
The core yarn is the foundation upon which the double covered yarn is built. The choice of fibers and the spinning process used to create the core yarn have a significant impact on the final characteristics of the double covered yarn.
- Fiber Selection: The core yarn can be made from a variety of natural or synthetic fibers, including cotton, wool, silk, polyester, and more. Each fiber type brings unique properties to the table, influencing the overall strength, durability, and hand feel of the final fabric.
- Spinning Technique: The spinning process used to create the core yarn, such as ring spinning, open-end spinning, or air-jet spinning, determines the yarn’s twist level, thickness, and overall structural integrity.
The Role of the Covering Yarns
The two layers of covering yarns, wrapped around the core, serve to enhance the yarn’s performance and aesthetic qualities.
- First Covering Yarn: The first layer of covering yarn is responsible for adding immediate visual appeal, softness, and a smooth surface to the double covered yarn. This layer can be made from finer, more delicate fibers, creating a luxurious hand feel.
- Second Covering Yarn: The second layer of covering yarn further reinforces the yarn’s structure, contributing to its durability and resistance to abrasion. This layer can be made from slightly coarser fibers, providing additional strength and stability.
Manufacturing Double Covered Yarn: A Detailed Process Breakdown
The creation of double covered yarn is a meticulous dance of machinery and human expertise, involving a series of carefully choreographed processes.
Preparation: Laying the Foundation
The journey begins with the source material – the fibers that will be transformed into yarns. These fibers undergo a series of treatments, including cleaning, blending, and carding, to ensure uniform quality and prepare them for spinning.
Yarn Spinning: Twisting the Core
The prepared fibers are then fed into spinning machines, where they are twisted together to form the core yarn. This crucial step determines the core yarn’s thickness, twist level, and overall strength, which will ultimately impact the characteristics of the final double covered yarn.
First Covering: Adding the Initial Layer
The core yarn is then passed through the first covering machine. Here, a finer yarn, known as the covering yarn, is wrapped around the core, adding a layer of protection and creating a smoother, more substantial yarn.
Second Covering: Enhancing the Structure
The process is repeated, with the now-covered yarn being fed through another covering machine. This second layer of covering yarn provides additional benefits, further enhancing the yarn’s aesthetic appeal, durability, and overall handle.
Finishing: The Final Touch
The double covered yarn undergoes a series of finishing treatments, such as heat setting, calendaring, and dyeing, to optimize its performance and impart the desired aesthetic properties.
Choosing the Right Core and Cover Yarns for Optimal Performance
The specific type of core and covering yarns used in the manufacturing process can greatly influence the final characteristics of the double covered yarn. Careful selection of these components is crucial to achieving the desired performance and aesthetic qualities.
Core Yarn Considerations
The choice of core yarn fibers and spinning techniques can have a significant impact on the overall strength, durability, and handle of the double covered yarn.
- Fiber Selection: Natural fibers like cotton, wool, and silk offer unique properties, while synthetic fibers like polyester and nylon provide enhanced strength and stretch.
- Spinning Techniques: The core yarn’s twist level, thickness, and structural integrity are determined by the spinning process, which can range from ring spinning to air-jet spinning.
Covering Yarn Considerations
The covering yarns play a crucial role in enhancing the double covered yarn’s visual appeal, softness, and durability.
- Fiber Composition: The covering yarns can be made from finer, more delicate fibers to create a luxurious hand feel, or coarser fibers to provide additional strength and stability.
- Yarn Structure: The covering yarns can be single-ply or multi-ply, further influencing the final characteristics of the double covered yarn.
The Advantages of Using Double Covered Yarn: From Strength to Aesthetics
Double covered yarn possesses a captivating blend of characteristics that make it a prized option in textile manufacturing.
Enhanced Durability
The two layers of covering yarns significantly increase the yarn’s resistance to abrasion, tearing, and pilling, resulting in fabrics that hold their shape and maintain their integrity over time.
Luxurious Hand Feel
The smooth, tightly-woven construction of double covered yarn translates into fabrics that feel soft, luxurious, and comfortable against the skin. The second layer of covering yarn amplifies this quality, contributing to a richer and more decadent drape.
Versatile Aesthetics
Double covered yarn allows for a wide range of visual textures, from subtle, almost invisible twists to intricate decorative patterns. This versatility enables fabric designers to create fabrics with captivating surfaces that add depth and interest to garments and upholstery.
Enhanced Performance
The tightly woven structure of double covered yarn enhances fabric performance in various ways. It increases the fabric’s resistance to wrinkles, provides excellent drape, and improves its dimensional stability, ensuring a more refined and longer-lasting finish.
Applications of Double Covered Yarn: Where it Excels
Double covered yarn is a chameleon in the textile world, seamlessly adapting to a wide range of applications, from the realm of fashion to the realm of industry.
Apparel
Double covered yarn finds its home in clothing ranging from casual T-shirts to luxurious evening gowns. Its durability and softness make it ideal for fabrics that require frequent laundering, while its versatility enables designers to create sophisticated textures and patterns.
Home Furnishings
Double covered yarn graces the world of home furnishings, adding elegance and longevity to upholstery fabrics, curtains, and bed linens. Its luxurious hand feel contributes to a sense of comfort and sophistication in the home environment.
Industrial Textiles
Double covered yarn also plays a vital role in the realm of industrial textiles, where its durability and resistance to wear provide indispensable qualities for applications such as luggage straps, upholstery for public transportation, and automotive fabric.
Technical Textiles
This yarn’s versatility extends to technical textiles, where its consistent properties and ability to withstand stress make it suitable for applications in filtration membranes, protective gear, and even medical textiles.
Quality Control in Double Covered Yarn Production: Ensuring Excellence
Maintaining consistent quality is of utmost importance in the manufacturing of double covered yarn. Rigorous quality control measures are implemented throughout the production process to ensure the final product meets the highest standards.
Raw Material Inspection
The initial inspection of the raw materials, including the core and covering yarns, is crucial. This step ensures that the fibers and yarns used in the manufacturing process meet the established specifications and quality benchmarks.
Process Monitoring
At each stage of the production, from fiber preparation to the final finishing, the manufacturing process is closely monitored. This includes regular checks on parameters such as twist levels, yarn tension, and machine settings to maintain consistent quality.
Testing and Evaluation
Comprehensive testing and evaluation are conducted on the double covered yarn, both during and after the manufacturing process. This includes evaluating the yarn’s physical properties, such as strength, abrasion resistance, and color fastness, to ensure it meets the desired performance standards.
Continuous Improvement
The commitment to quality is an ongoing effort, with manufacturers constantly seeking ways to refine and improve their processes. This may involve incorporating new technologies, implementing lean manufacturing techniques, or collaborating with industry experts to stay at the forefront of innovation.
Trends and Innovations in Double Covered Yarn Manufacturing
The world of textiles is constantly evolving, and double covered yarn continues to adapt and innovate to meet the changing demands of the market.
Sustainability
As sustainability becomes an increasingly pressing concern, manufacturers are exploring ways to develop double covered yarns from recycled materials and fibers produced through eco-conscious processes. This includes utilizing sustainable fibers like organic cotton, bamboo, and recycled polyester.
Performance Enhancement
Technological advancements are leading to double covered yarn innovations that enhance performance. This includes the development of yarns treated with water-repelling coatings or incorporating high-tech fibers to offer improved stretch, breathability, and thermal regulation.
Customization and Personalization
Consumers are seeking greater customization in their textiles, and double covered yarn is well-suited to address this demand. Manufacturers are offering a wider range of color combinations, intricate textures, and personalized designs to cater to individual preferences.
The Future of Double Covered Yarn: Exploring Emerging Possibilities
As the textile industry continues to evolve, the future of double covered yarn holds immense potential. Technological advancements, consumer trends, and sustainable practices will shape the direction of this versatile yarn.
Advancements in Manufacturing Techniques
Innovations in spinning, covering, and finishing processes will likely lead to the development of even more sophisticated double covered yarns, offering enhanced performance, improved efficiency, and reduced environmental impact.
Incorporation of Smart Technologies
The integration of smart technologies, such as embedded sensors or conductive fibers, into double covered yarns could pave the way for the creation of intelligent textiles with enhanced functionalities, opening up new applications in fields like healthcare, sports, and beyond.
Embracing Circular Economy Principles
As the demand for sustainable textiles continues to grow, double covered yarn manufacturers will increasingly focus on incorporating circular economy principles. This may involve the development of closed-loop recycling systems, the use of biodegradable or compostable fibers, and the exploration of innovative dyeing and finishing techniques.
Conclusion
Double covered yarn stands as a testament to the ingenuity of textile manufacturing, combining traditional techniques with cutting-edge technology to create yarns with exceptional characteristics. Its durability, luxurious hand feel, versatility, and performance make it a cornerstone of the textile industry, ensuring its continued relevance in the ever-evolving world of fabrics. As technology advances and sustainability becomes increasingly essential, we can expect to see even more exciting innovations within the realm of double covered yarns, ensuring that this intricate and valuable thread continues to weave its magic into the tapestry of our lives.