Rubber covered yarn, a unique textile innovation, combines the elasticity of rubber with the strength and versatility of traditional yarns. This hybrid material has revolutionized various industries, from fashion to industrial applications, by offering enhanced durability, flexibility, and performance. In this comprehensive article, we’ll explore the intricacies of rubber covered yarn, its production process, and its myriad applications across different sectors.
Rubber Covered Yarn
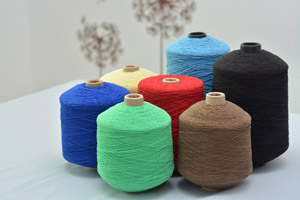
Rubber covered yarn represents a fascinating fusion of natural and synthetic materials, offering a unique combination of properties that make it invaluable in numerous applications. This innovative textile product consists of a core yarn, typically made from materials like polyester, nylon, or cotton, encased in a rubber coating.
The Composition of Rubber Covered Yarn
Rubber covered yarn is composed of two primary elements:
The core yarn forms the foundation of the product, providing strength and structure. This core can be made from a variety of materials, each chosen for specific properties and end-use requirements. Common core materials include:
- Polyester: Known for its durability and resistance to stretching, polyester cores are often used in applications requiring dimensional stability.
- Nylon: Valued for its strength and elasticity, nylon cores are ideal for products that need to withstand repeated stretching and compression.
- Cotton: Offering breathability and comfort, cotton cores are frequently used in applications where skin contact is a consideration.
The rubber coating envelops the core yarn, imparting unique properties to the final product. This coating can be made from various types of rubber, including:
- Natural rubber: Derived from the sap of rubber trees, natural rubber offers excellent elasticity and resilience.
- Synthetic rubbers: Such as neoprene or silicone, these man-made alternatives can provide specific properties like chemical resistance or heat tolerance.
Manufacturing Process of Rubber Covered Yarn
The production of rubber covered yarn involves a sophisticated process that requires precision and expertise:
- Core Preparation: The selected core yarn is carefully wound onto bobbins or spools, ensuring even tension and distribution.
- Rubber Compounding: The rubber coating material is prepared by mixing raw rubber with various additives to enhance its properties. These additives may include vulcanizing agents, antioxidants, and colorants.
- Extrusion Coating: The core yarn is fed through an extruder where the rubber compound is applied under high pressure and temperature. This process ensures a uniform coating around the core.
- Vulcanization: The coated yarn undergoes a vulcanization process, typically using heat or chemical agents, to cross-link the rubber molecules. This step is crucial for enhancing the rubber’s strength, elasticity, and durability.
- Cooling and Finishing: The vulcanized rubber covered yarn is cooled and may undergo additional treatments such as lubricant application or surface texturing, depending on the intended use.
Applications of Rubber Covered Yarn
The unique properties of rubber covered yarn make it suitable for a wide range of applications:
Textile Industry:
- Elastic waistbands and cuffs in clothing
- Compression garments for medical and athletic use
- Swimwear and activewear fabrics
Industrial Uses:
- Conveyor belts and power transmission belts
- Automotive hoses and seals
- Vibration dampening in machinery
Sports Equipment:
- Tennis racket strings
- Golf club grips
- Exercise resistance bands
By combining the strength of traditional yarns with the elasticity and resilience of rubber, rubber covered yarn has opened up new possibilities in product design and functionality across various industries.
Rubber Coated Yarn
Rubber coated yarn, often used interchangeably with rubber covered yarn, refers to a specialized textile product where a base yarn is encased in a layer of rubber. This innovative material combines the best properties of both components, resulting in a versatile product with enhanced characteristics.
Understanding Rubber Coated Yarn
Rubber coated yarn is essentially a composite material consisting of two main components:
The base yarn forms the core of the product and can be made from various materials such as:
- Polyester: Chosen for its strength and dimensional stability
- Nylon: Valued for its durability and elasticity
- Cotton: Preferred for its comfort and breathability
The rubber coating envelops the base yarn, providing additional properties like:
- Elasticity: The rubber layer adds stretchability to the yarn
- Water resistance: Many rubber coatings offer protection against moisture
- Improved grip: The rubber surface can enhance friction and gripping properties
Production Techniques for Rubber covered Yarn
The manufacturing process of rubber coated yarn involves several sophisticated steps:
- Yarn Preparation: The base yarn is carefully selected and prepared, ensuring it’s free from defects and impurities.
- Rubber Compound Formulation: A specific rubber compound is created, tailored to the desired properties of the final product. This may involve mixing natural or synthetic rubbers with various additives.
- Coating Application: The rubber coating is applied to the base yarn through one of several methods:
- Dip Coating: The yarn is passed through a bath of liquid rubber compound.
- Extrusion Coating: The rubber is extruded around the yarn in a continuous process.
- Spray Coating: A fine mist of rubber compound is sprayed onto the yarn surface.
- Curing Process: The coated yarn undergoes a curing or vulcanization process, typically involving heat treatment, to set the rubber coating and enhance its properties.
- Finishing and Quality Control: The rubber coated yarn may undergo additional treatments and is subjected to rigorous quality checks to ensure it meets specifications.
Advantages of Rubber covered Yarn
Rubber coated yarn offers several benefits that make it a preferred choice in various applications:
Enhanced Durability: The rubber coating provides an extra layer of protection to the base yarn, increasing its resistance to wear and tear. This makes rubber coated yarn ideal for applications where longevity is crucial, such as in industrial machinery or outdoor equipment.
Improved Elasticity: The rubber component adds significant stretch and recovery properties to the yarn. This elasticity is particularly valuable in textile applications, allowing for the creation of form-fitting garments or flexible components in industrial products.
Water and Chemical Resistance: Many rubber coatings offer excellent resistance to water and various chemicals. This property is essential in applications where the yarn may be exposed to harsh environments or frequent washing.
By combining the strengths of traditional yarns with the unique properties of rubber, rubber coated yarn has become an indispensable material in numerous industries, driving innovation and improving product performance across a wide spectrum of applications.
What is Rubber Fabric
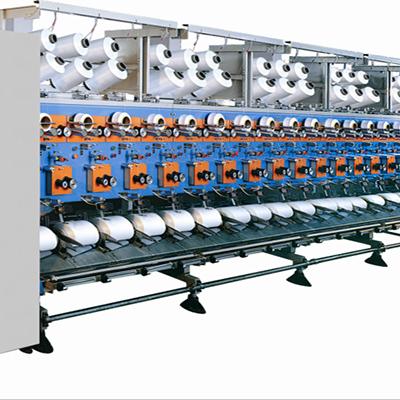
Rubber fabric, a versatile and innovative material, represents a fascinating intersection of textile technology and rubber engineering. This unique product combines the flexibility and comfort of traditional fabrics with the distinctive properties of rubber, resulting in a material that offers a wide range of applications across various industries.
Defining Rubber Fabric
Rubber fabric is a composite material that typically consists of two main components:
- The Base Fabric: This forms the foundation of the material and can be made from various textile fibers such as:
- Cotton
- Polyester
- Nylon
- Spandex
- The Rubber Component: This can be applied in different ways:
- As a coating on one or both sides of the fabric
- Embedded within the fabric structure
- As rubber threads or yarns woven or knitted into the fabric
The combination of these elements results in a material that retains the basic structure and feel of fabric while incorporating the unique properties of rubber.
Types of Rubber Fabric
Rubber fabric comes in various forms, each designed for specific applications:
Rubberized Fabric: This type features a layer of rubber applied to one or both sides of a traditional fabric. It’s commonly used in waterproof clothing and industrial applications.
Rubber-Infused Fabric: In this variant, rubber or elastic fibers are integrated into the fabric structure during the weaving or knitting process. This creates a stretchable, form-fitting material often used in sportswear and compression garments.
Neoprene Fabric: A synthetic rubber material that’s often bonded to fabric on one or both sides. It’s known for its insulation properties and is widely used in wetsuits and protective gear.
Properties of Rubber Fabric
Rubber fabric exhibits a unique combination of properties that make it suitable for a wide range of applications:
Elasticity and Flexibility: The rubber component imparts significant stretch and recovery properties to the fabric, allowing it to conform to shapes and return to its original form.
Water Resistance: Many rubber fabrics offer excellent water repellency or waterproofing, making them ideal for outdoor and marine applications.
Durability: The addition of rubber often enhances the fabric’s resistance to wear and tear, increasing its lifespan in demanding environments.
Insulation: Some rubber fabrics, particularly neoprene, provide excellent thermal insulation, making them suitable for protective clothing and gear.
Chemical Resistance: Certain types of rubber fabrics offer resistance to various chemicals, oils, and solvents, making them valuable in industrial and laboratory settings.
Applications of Rubber Fabric
The versatile nature of rubber fabric has led to its adoption in numerous fields:
Apparel and Fashion:
- Sportswear and activewear
- Raincoats and waterproof clothing
- Compression garments for athletics and medical use
Industrial Uses:
- Protective clothing for workers
- Conveyor belts and industrial seals
- Automotive interiors and seating
Marine and Outdoor Equipment:
- Wetsuits and diving gear
- Inflatable boats and rafts
- Camping equipment and tents
Medical and Healthcare:
- Hospital bedding and mattress covers
- Surgical gowns and protective equipment
- Orthopedic supports and braces
By combining the comfort and versatility of fabric with the unique properties of rubber, rubber fabric has become an indispensable material in modern manufacturing and design. Its ability to meet diverse requirements across multiple industries highlights its importance as an innovative and adaptable material in today’s world.
Is Rubber a Textile Material
The question of whether rubber is a textile material is intriguing and requires a nuanced understanding of both rubber and textile definitions. While rubber itself is not traditionally classified as a textile, its increasing integration with fabric and its use in textile-like applications has blurred the lines between these categories.
Defining Textiles and Rubber
To address this question, let’s first define both textiles and rubber:
Textiles: Textiles are typically defined as flexible materials made by weaving, knitting, felting, or bonding fibers. These fibers can be natural (like cotton or wool) or synthetic (like polyester or nylon). The key characteristic of textiles is their fibrous structure and the methods used to create them.
Rubber: Rubber is an elastic material derived either naturally from the latex of certain plants or synthetically produced. It’s known for its elasticity, water resistance, and ability to return to its original shape after being stretched or compressed.
The Intersection of Rubber and Textiles
While rubber in its pure form is not considered a textile, there are several ways in which rubber and textiles intersect:
Rubber-Coated Fabrics: Many textiles are coated or impregnated with rubber to enhance their properties. These materials, while fundamentally textile-based, incorporate rubber as a significant component.
Rubber Threads and Yarns: Elastic threads made from rubber or rubber-like materials (such as spandex) are often incorporated into textile structures, creating stretchy fabrics.
Neoprene and Similar Materials: Synthetic rubbers like neoprene are often bonded to fabric layers, creating a material that has characteristics of both textiles and rubber.
Arguments for Considering Rubber as a Textile Material
While rubber doesn’t fit the traditional definition of a textile, there are arguments for considering it as part of the broader textile family:
Functionality: In many applications, rubber-based materials serve functions similar to traditional textiles, such as in clothing, upholstery, and industrial fabrics.
Manufacturing Processes: Some rubber products, particularly those incorporating fabric reinforcement, are manufactured using processes similar to textile production.
Industry Classification: In certain contexts, particularly in industrial and technical applications, rubber-based materials are often grouped with textiles under broader categories like “flexible materials” or “technical textiles.”
Arguments Against Considering Rubber as a Textile Material
However, there are also strong reasons to maintain a distinction between rubber and textiles:
Material Structure: Rubber lacks the fibrous structure that is fundamental to the definition of textiles.
Production Methods: The primary methods of producing rubber (such as molding or extrusion) are distinct from traditional textile manufacturing techniques.
Material Properties: While rubber can be made flexible like textiles, its core properties (elasticity, impermeability) are fundamentally different from those of typical textile fibers.
The Evolving Definition of Textiles
It’s important to note that the definition of textiles is evolving with technological advancements:
Technical Textiles: This growing field includes materials that may not fit traditional textile definitions but serve similar functions. Rubber-based materials often fall into this category.
Composite Materials: Many modern materials blur the lines between different material categories, combining properties of textiles, plastics, and elastomers.
Practical Implications
The classification of rubber in relation to textiles has practical implications:
Industry Standards: Different standards and regulations may apply depending on whether a material is classified as a textile or a rubber product.
Research and Development: Understanding the relationship between rubber and textiles can lead to innovative hybrid materials that combine the best properties of both.
Market Positioning: How a material is classified can affect its marketing and perceived value in different industries.
While rubber in its pure form is not traditionally considered a textile material, its increasing integration with fabrics and its use in textile-like applications have created a gray area in classification. The answer to whether rubber is a textile material often depends on the specific context and application. As materials science continues to advance, the boundaries between different material categories are likely to become even more fluid, challenging traditional definitions and opening up new possibilities for innovative products.
Rubber Coating Process
The rubber coating process is a sophisticated industrial technique used to apply a layer of rubber or rubber-like material to various substrates, including fabrics, metals, and other materials. This process enhances the properties of the base material, adding characteristics such as elasticity, water resistance, and durability. Understanding the intricacies of the rubber coating process is crucial for manufacturers and engineers working in industries ranging from textiles to automotive.
Overview of Rubber Coating
Rubber coating involves applying a layer of rubber or rubber-based compound to a substrate material. The process can be tailored to achieve specific properties in the final product, such as:
- Improved grip and friction
- Water and chemical resistance
- Electrical insulation
- Vibration dampening
- Enhanced durability and wear resistance
The choice of rubber compound and coating method depends on the intended application and the properties required in the final product.
Types of Rubber Used in Coating
Various types of rubber can be used in the coating process, each offering unique properties:
Natural Rubber: Derived from latex, natural rubber offers excellent elasticity and resilience. It’s often used in applications requiring high stretch and recovery.
Synthetic Rubbers: These include materials like:
- Neoprene: Known for its chemical and weather resistance
- Silicone: Offers high temperature resistance and flexibility
- Nitrile: Provides excellent oil and fuel resistance
Thermoplastic Elastomers (TPEs): These materials combine the properties of rubber with the processability of plastics, offering versatility in manufacturing.
Preparation of Rubber Compounds
Before the coating process begins, the rubber compound must be prepared:
- Compounding: Raw rubber is mixed with various additives such as:
- Vulcanizing agents
- Antioxidants
- Fillers
- Plasticizers
- Colorants
- Mastication: The rubber compound is mechanically worked to reduce its viscosity and improve its processability.
- Calendering or Extrusion: The compound is formed into sheets or extruded into the desired form for the coating process.
Substrate Preparation
Proper preparation of the substrate is crucial for achieving a strong bond between the rubber coating and the base material:
Surface Cleaning: The substrate is thoroughly cleaned to remove any dirt, oils, or contaminants that could interfere with adhesion.
Surface Treatment: Depending on the substrate, various treatments may be applied:
- Chemical etching
- Plasma treatment
- Primer application
These treatments enhance the surface energy of the substrate, promoting better adhesion of the rubber coating.
Rubber Coating Methods
Several methods can be employed to apply rubber coatings, each suited to different applications:
Dip Coating: The substrate is immersed in a liquid rubber compound and then withdrawn at a controlled rate. This method is often used for gloves, small parts, and some textiles.
Process:
- The substrate is dipped into a tank of liquid rubber compound.
- The coated substrate is slowly withdrawn, allowing excess material to drain.
- The coating is then cured, often through heat treatment.
Advantages:
- Uniform coating thickness
- Suitable for complex shapes
- Can coat both interior and exterior surfaces
Spray Coating: Liquid rubber is atomized and sprayed onto the substrate. This method is versatile and can be used for large or irregularly shaped objects.
Process:
- The rubber compound is thinned to a sprayable consistency.
- It’s sprayed onto the substrate using specialized equipment.
- Multiple layers may be applied to achieve the desired thickness.
- The coating is cured through heat or air drying.
Advantages:
- Flexible application on various surfaces.
- Easier to control coating thickness by adjusting spray parameters.
- Suitable for large-scale production.
Curing and Finishing
After the rubber has been applied, it’s essential to cure it properly. Curing involves a chemical reaction that transforms the raw rubber into a stable, durable material. The curing process can vary based on the type of rubber used and the intended application.
Heat Curing: This is one of the most common methods where the coated product is subjected to elevated temperatures for a specific duration. This accelerates the vulcanization process, leading to improved elasticity and strength.
Chemical Curing: In some cases, reactive chemicals are added to the rubber compound before application. These chemicals initiate a curing reaction once the rubber is applied to the substrate, allowing for a more flexible manufacturing process.
Finishing Steps: Once cured, additional finishing processes may be implemented, including trimming excess material, surface treatment for improved aesthetics, or applying secondary coatings for added properties like UV resistance.
What Material Is Rubber?
Rubber is a versatile material known for its unique elastic properties, derived from both natural and synthetic sources. To fully understand what constitutes rubber as a material, we need to explore its origins, types, and characteristics.
Natural Rubber
Natural rubber is primarily obtained from the latex sap of the rubber tree (Hevea brasiliensis). It is a polymer composed mainly of polyisoprene, which provides excellent elasticity.
Characteristics: Natural rubber boasts remarkable tensile strength, flexibility, and resilience, making it ideal for many applications, including tires, seals, and medical devices.
Sourcing: The harvesting process involves tapping into the bark of rubber trees, allowing collectors to obtain the milky latex without harming the tree, thus promoting sustainable practices.
Synthetic Rubber
Synthetic rubber is produced through the polymerization of monomers such as butadiene and styrene. There are several types of synthetic rubber, each tailored for specific applications.
Types of Synthetic Rubber:
- Styrene-Butadiene Rubber (SBR): Commonly used in tire manufacturing due to its superior wear resistance and aging stability.
- Neoprene: Valued for its weather resistance and durability, neoprene is widely used in outdoor gear and industrial applications.
- Nitrile Rubber: Known for its excellent oil and fuel resistance, nitrile rubber is essential in automotive sealing and gaskets.
Properties of Rubber
Understanding the properties of rubber aids in comprehending its versatility as a material:
Elasticity: Rubber can stretch significantly without permanent deformation, allowing it to return to its original shape after being stretched or compressed. This property is paramount in applications requiring cushioning or shock absorption.
Durability: Rubber’s inherent resistance to wear and tear, as well as its ability to withstand various environmental conditions (UV rays, ozone, chemicals), enhances its longevity in numerous products.
Thermal Stability: Depending on the formulation, certain types of rubber can withstand high temperatures, making them suitable for applications in automotive and aerospace industries.
Environmental Considerations
With increasing awareness regarding environmental sustainability, the rubber industry faces challenges related to sourcing and disposal.
Sustainable Practices: Efforts to promote natural rubber cultivation focus on responsible forestry management and minimizing deforestation. Additionally, some companies are investing in synthetic alternatives with reduced environmental impact.
Recycling: Rubber recycling poses challenges due to the cross-linking nature of vulcanized rubber. However, advancements in recycling technologies are enabling the recovery of rubber for new applications, reducing waste.
Conclusion
In conclusion, rubber-covered yarn, rubber-coated yarn, and the diverse aspects of rubber as a material highlight the dynamic intersection between traditional textiles and innovative materials. From understanding the nuances of rubber coating processes to exploring the evolving definitions of textiles, it’s evident that rubber plays a significant role in modern manufacturing and design.
As technology continues to advance, traditional boundaries will blur, fostering new possibilities in material science. The integration of rubber into textiles opens doors to innovative applications, whether in protective clothing, automotive components, or everyday consumer goods. Understanding these materials and their properties not only enriches our knowledge but also empowers us to make informed choices in design, production, and consumption.
Furthermore, the classification debate surrounding rubber and textiles emphasizes the importance of adaptability and evolution in materials science. As industries evolve, so too must our understanding of what constitutes a textile material, paving the way for hybrid solutions that cater to the demands of contemporary applications.
Thus, the exploration of rubber and its relationship with textiles not only enriches our comprehension of material science but also encourages creativity and innovation in future designs and applications. Whether through rubber-coated fabrics or advanced elastomeric composites, the potential remains vast, promising exciting developments in the world of materials.
One Response