Rubber covered yarn is increasingly becoming a staple in various industries, from textile manufacturing to engineering applications. This specialized material offers unique properties such as elasticity, durability, and resistance to various environmental factors, which makes it an ideal choice in many scenarios. The process of understanding rubber covered yarn involves a comprehensive exploration of its production, its applications, and the machinery involved in its manufacturing, enriching our insight into its importance in modern-day manufacturing practices.
Rubber covered yarn
When delving into the intricate world of rubber covered yarn, it is crucial first to appreciate its composition and properties. This material typically consists of a core yarn that is encased in a layer of rubber, enhancing its overall performance characteristics. The end product is a flexible and resilient yarn that can withstand high levels of tension and strain, making it highly suitable for a range of uses.
Rubber covered yarn serves multiple functions, but its primary role is to provide strength and elasticity to textiles. It is widely utilized in specialized applications, including the production of elastic materials, bands, and various types of reinforced fabrics. The process of covering the yarn with rubber lends additional benefits, such as moisture resistance, which is essential for items that may be exposed to wet conditions. This increase in durability translates to a longer lifespan of the products made from rubber-covered yarn.
In addition to strength and durability, one of the most remarkable attributes of rubber covered yarn is its ability to maintain flexibility. This feature is paramount, especially in applications requiring movement. For instance, in the garment industry, clothes that incorporate this type of yarn can offer enhanced comfort and fit. Consequently, understanding the production techniques and machinery used in creating rubber covered yarn is essential to appreciating its value across various sectors.
The Technology Behind Rubber Covered Yarn Production
The technology behind making rubber covered yarn is a fascinating intersection of traditional textile engineering and modern mechanical innovations. One of the key components in the production process is the rubber yarn covering machine, which is specifically designed for this purpose.
These machines operate by taking a core yarn, typically made of fibers like polyester, nylon, or cotton, and applying a layer of rubber over it. This process can be achieved through various means, including extrusion or coating application methods. The choice of technique often depends on the desired properties of the end product, highlighting the importance of aligning production methods with the intended use of the yarn.
The machinery involved in producing rubber covered yarn has advanced remarkably over the years. Modern rubber yarn covering machine manufacturers utilize computerized systems to ensure precision in applying the rubber coating. This peak in technology guarantees consistency in the final product, reducing wastage and ensuring that each batch meets the expected quality standards.
As the demand for rubber covered yarn continues to grow, the manufacturers are pushed to innovate further, making their machines more efficient while simultaneously investing in researching sustainable materials. Companies now regularly explore eco-friendly alternatives to traditional rubber, aiming to lessen the environmental impact while maintaining physical integrity.
Properties and Performance of Rubber Covered Yarn
Understanding the properties of rubber covered yarn goes beyond its basic composition. It is essential to analyze how these properties translate into real-world performance. One of the standout aspects is its mechanical strength, which directly affects the durability and reliability of the end products made from it.
Mechanical strength is often evaluated through stress and strain testing, providing insights on how the yarn performs under various loads. The elastic properties of rubber provide remarkable flexibility, allowing the yarn to stretch while retaining its original shape. This indicates not only its function in elastics but also its suitability for applications where movement is a constant factor.
Moreover, rubber covered yarn exhibits excellent resistance to environmental stressors, including moisture and chemical exposure. Such resistance makes it a desirable candidate for products in industries such as automotive, where resistance to water and wear is paramount. The elasticity of the rubber combined with the strength of the core yarn creates a robust product capable of withstanding harsh conditions.
The interaction of these properties results in a unique performance profile that exceeds that of standard yarns. For instance, in sports clothing, where both breathability and stretch are necessary, the incorporation of rubber covered yarn can create athletic wear that not only allows for movement but also enhances comfort.
What is rubber fabric
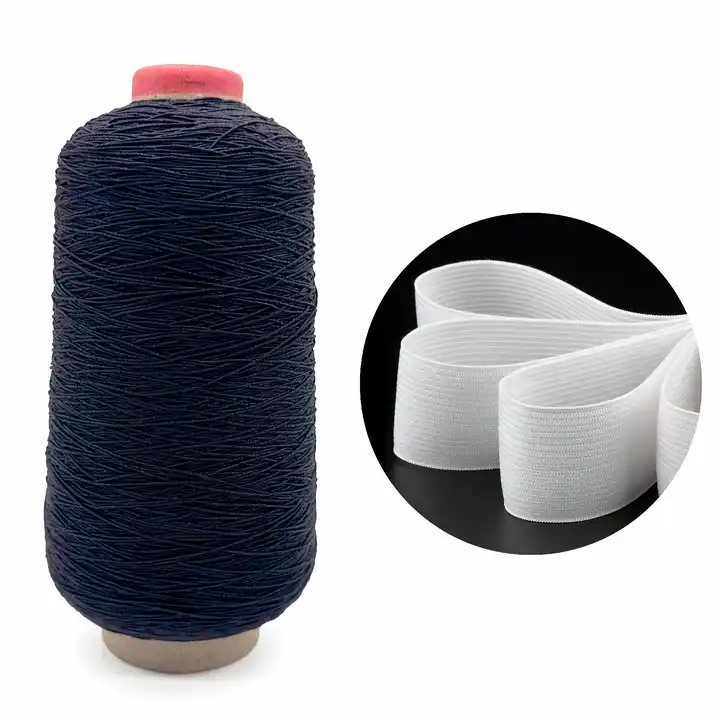
Rubber fabric is a unique material that marries the properties of rubber with traditional fabrics, resulting in a versatile product. Its creation typically involves the process of coating fabric with rubber or weaving rubber threads into the textile itself. This innovative approach provides a new layer of utility to traditional fabric, allowing it to be applied in various industries.
One of the most notable attributes of rubber fabric is its waterproof nature. This quality makes it particularly popular in the production of outdoor gear, raincoats, and various types of protective clothing. The added layer of rubber not only repels water but also provides insulation, making it ideal for cold-weather gear.
Additionally, the durability of rubber fabric is evident in its resistance to abrasions and various chemical substances. These properties are especially beneficial in workplaces where employees may come into contact with harsh materials or work in wet environments. Therefore, rubber fabric fulfills both safety and practicality in its applications.
While many recognize rubber fabric as simply a blend of rubber and textiles, the technicalities behind its production and the science of the materials involved invite a deeper exploration. It becomes evident that the interplay between various fibrous materials and rubber polymers results in a final product that is far more advanced than one might initially presume.
The Manufacturing Process of Rubber Fabric
The manufacturing process of rubber fabric is a multifaceted endeavor that integrates textile technology with rubber processing techniques. The journey of creating this material typically begins with selecting the appropriate base fabric, which may vary depending on the intended use.
Once the base fabric is determined, it undergoes a Pre-treatment stage where the fibers may be treated to enhance adhesion. The choice of chemical treatments can affect the ultimate performance of the rubber fabric, so selecting the right combinations is paramount. After pre-treatment, the fabric enters the rubber application stage, where either a coating or a lamination process is employed. This is where the rubber is added to the fabric, thereby granting its defining characteristics.
The vulcanization process is another crucial aspect of rubber fabric manufacturing. By applying heat and pressure, the rubber undergoes a transformation that enhances its elasticity and durability. This stage is essential, as it solidifies the bond between the rubber and the fabric, ensuring that the final product retains its properties even after extensive use.
Finally, quality control measures come into play. Manufacturers evaluate the properties of the rubber fabric through rigorous testing, assessing factors such as tensile strength, elasticity, and water resistance. This attention to detail throughout the manufacturing process ensures that only the best products reach the market.
Applications of Rubber Fabric
The range of applications for rubber fabric is vast and diverse, showcasing its versatility. Industries ranging from fashion to industrial safety have adopted this innovative material, each tailoring its use to meet specific needs.
In the fashion industry, rubber fabric beautifully merges aesthetics with functionality. Designers increasingly experiment with rubber-coated textiles for creating stylish yet durable outerwear. The ability to craft waterproof and breathable garments aligns with contemporary demands for sustainable and practical fashion.
In industrial realms, rubber fabric finds its place in safety garments, such as gloves and aprons. Workers shielded from various substances benefit immensely from wearing gear made from this resilient material. Furthermore, its lightweight nature, combined with its protective attributes, ensures comfort in demanding work environments.
The automotive industry is another sector reaping the rewards of rubber fabric, utilizing it for interior components and seat covers. Its ability to withstand wear and tear, along with its resistance to stains, makes it an intelligent choice for vehicles that require both durability and style.
As technology and trends evolve, the potential uses for rubber fabric continue to expand. The ongoing exploration of new blends and manufacturing methods offers possibilities for innovative products in fields we may not have previously considered.
Rubber yarn covering machine manufacturer
The role of a rubber yarn covering machine manufacturer is pivotal in the production landscape of rubber covered yarn. These manufacturers innovate machinery that directly impacts the quality and efficiency of yarn production, ultimately shaping the industry.
Manufacturers specializing in rubber yarn covering machinery invest heavily in research and development to refine their products continually. The machinery they produce must not only adhere to stringent quality standards but also integrate the latest technological advances. Automation, for instance, plays a significant role in enhancing the precision and speed of the covering process, which in turn boosts output and reduces operational costs.
In the current climate of sustainability, many rubber yarn covering machine manufacturers are looking towards eco-friendly practices. This may involve designing machines that consume less energy or are compatible with biodegradable materials. The shift towards sustainable practices is not only timely but necessary, indicating a responsible approach to manufacturing and an acknowledgment of broader environmental implications.
Furthermore, partnerships between manufacturers and textile producers are increasingly common. Such collaborations aim to ensure that the machinery developed aligns precisely with the practical needs of production lines. This kind of synergy boosts innovation, merging traditional textile knowledge with modern machine capabilities to produce higher quality rubber covered yarn.
Innovation in Machinery
Innovation in machinery continues to transform the methods used in producing rubber covered yarn. These advancements mainly focus on improving efficiency and quality.
Modern machines are equipped with sophisticated controls that allow for real-time monitoring of production parameters. This capability enables operators to track various metrics throughout the covering process, ensuring consistent quality in finished products. Furthermore, automation prevents human error and reduces downtime, essential factors in an industry that demands high output.
The use of computer-aided design (CAD) in developing these machines allows for customizations catered to specific product requirements. Manufacturers can adapt their machines to accommodate varying widths, types of yarn, and rubber characteristics, showcasing flexibility in production options. This ability to tailor machinery to client specifications highlights a significant stride away from one-size-fits-all approaches.
Additionally, many new machines incorporate integrated safety features, allowing manufacturers and operators to adhere to best practices while protecting their workforce. By designing machines with user safety in mind, manufacturers showcase their commitment to maintaining a safe working environment.
Market Trends and Future Prospects
In examining the market trends concerning rubber yarn covering machines, significant changes reflect broader shifts in the textile industry. The increasing demand for rubber covered yarn has spurred manufacturers to consider market dynamics carefully. As sustainability becomes a priority across industries, machine manufacturers are adapting technologies to reduce waste and enhance the recyclability of materials.
Moreover, as industries continue to expand globally, the opportunity for rubber yarn covering machine manufacturers to enter new markets is significant. The adoption of advanced textile practices in emerging economies presents opportunities for growth while encouraging the sharing of innovative technology and methodologies.
As the industry evolves, manufacturers will need to remain agile, responding to trends while maintaining a focus on quality and performance. This adaptability will not only ensure competitiveness but also position them as leaders in innovation and sustainability.
Conclusion
Understanding the production of rubber covered yarn encompasses a detailed exploration of its properties, manufacturing processes, and the machinery that facilitates its creation. As industries evolve and demand for effective materials rises, rubber covered yarn remains a pivotal solution, offering durability, elasticity, and performance across various applications.
The synthesis of traditional textile practices with advanced technology creates a dynamic landscape for rubber covered yarn production. With continuous advancements in machinery, market trends leaning towards sustainability, and the versatility of rubber fabric, the future of this sector appears bright.
Both the manufacturers and the industries relying on rubber covered yarn must collaborate and innovate to meet emerging challenges, ensuring that they not only fulfill present demands but also pave the way for future developments in material science and engineering.
Through this comprehensive examination, a clearer understanding emerges, illustrating the significance of rubber covered yarn and its ongoing impact across multiple domains of industry and fashion.
Support by us